Tackling Common Defects in Die Casting
Jul 18, 2023
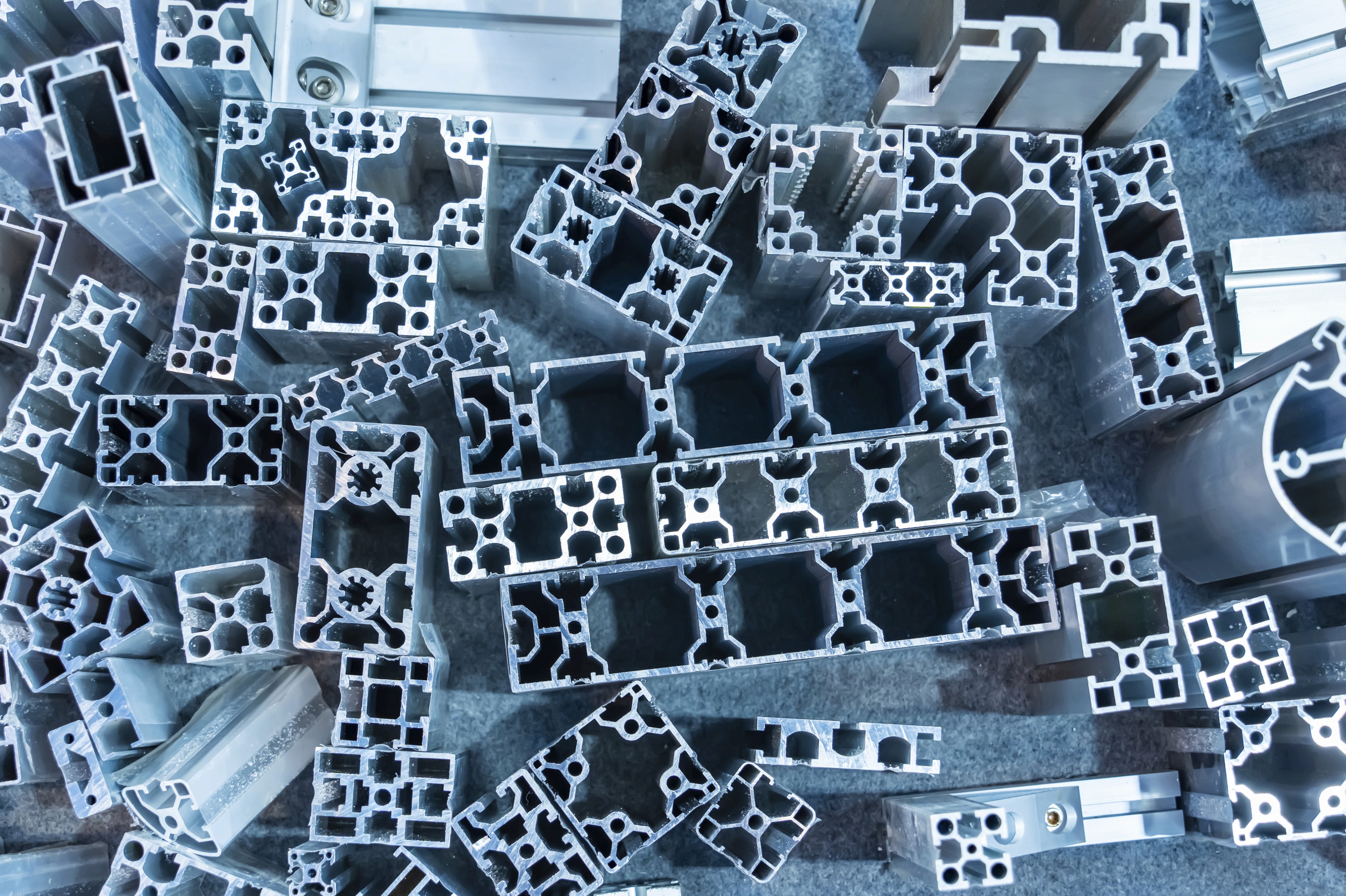
Die casting is a go-to manufacturing process when the goal is to mass-produce intricate designs with pinpoint precision. While this process is chock-full of advantages, it's not free from its challenges. The potential defects in die-cast parts are an ongoing concern for manufacturers. However, a thorough understanding of these potential pitfalls - their origins, implications, and mitigation strategies - can elevate the quality of the casting process and improve outcomes across the board.
Porosity
Cause: Porosity refers to tiny voids or cavities that emerge when air or gas becomes trapped within the solidifying metal. Abrupt cooling, uncontrolled flow of molten metal, or inefficient venting can contribute to this flaw.
Solution: Enhancing the design of the venting and gating systems can largely mitigate porosity. Slow and steady pouring combined with a managed cooling rate also plays a pivotal role in reducing this defect.
Blistering
Cause: Blisters are raised imperfections that manifest on the die-cast part's surface when pockets of trapped air or gas expand. This is usually triggered by post-casting heat treatments.
Solution: Minimizing turbulence during casting and ensuring thorough mold filling can stave off blisters. Refining the gating system bolsters the integrity of the final product and further reduces the chances of blistering.
Flash
Cause: Flash defects appear as unwanted thin extensions of metal along the mold's parting line. They arise when molten metal infiltrates spaces between mold halves, or around ejector pins or slide interfaces.
Solution: Regular mold maintenance, applying the correct clamping force, and finely tuning the casting conditions are pivotal to keeping flash defects at bay.
Cold Shut
Cause: Recognized by lines or minor cracks on the part's surface, cold shuts happen when two streams of molten metal meet inside the mold but fail to fuse seamlessly.
Solution: By making adjustments such as tweaking mold temperature, amplifying the plunger speed, or repositioning the gate, manufacturers can effectively counteract cold shuts.
Misruns
Cause: Misruns are characterized by molten metal's failure to satisfactorily fill the mold cavity. This results in parts with thin sections or areas that remain unfilled.
Solution: Raising the temperature of both the molten metal and the mold ensures superior metal flow, facilitating complete filling of the cavity and preventing misruns.
Hot Tears
Cause: Also known as hot cracks, these irregular-shaped fissures emerge as the metal undergoes cooling and solidification. They're birthed from internal stress due to constrained shrinkage during this phase.
Solution: Employing molds with even thickness, fine-tuning cooling rates, and selecting alloys with favorable characteristics can significantly reduce the occurrence of hot tears.
Recognizing and understanding these most common defects is in many cases all it takes to avoid them and achieve optimal results in die casting. By addressing the underlying causes of these issues and applying corrective measures, manufacturers can enhance the die casting process and consistently deliver products that meet the stringent quality standards their clients expect.
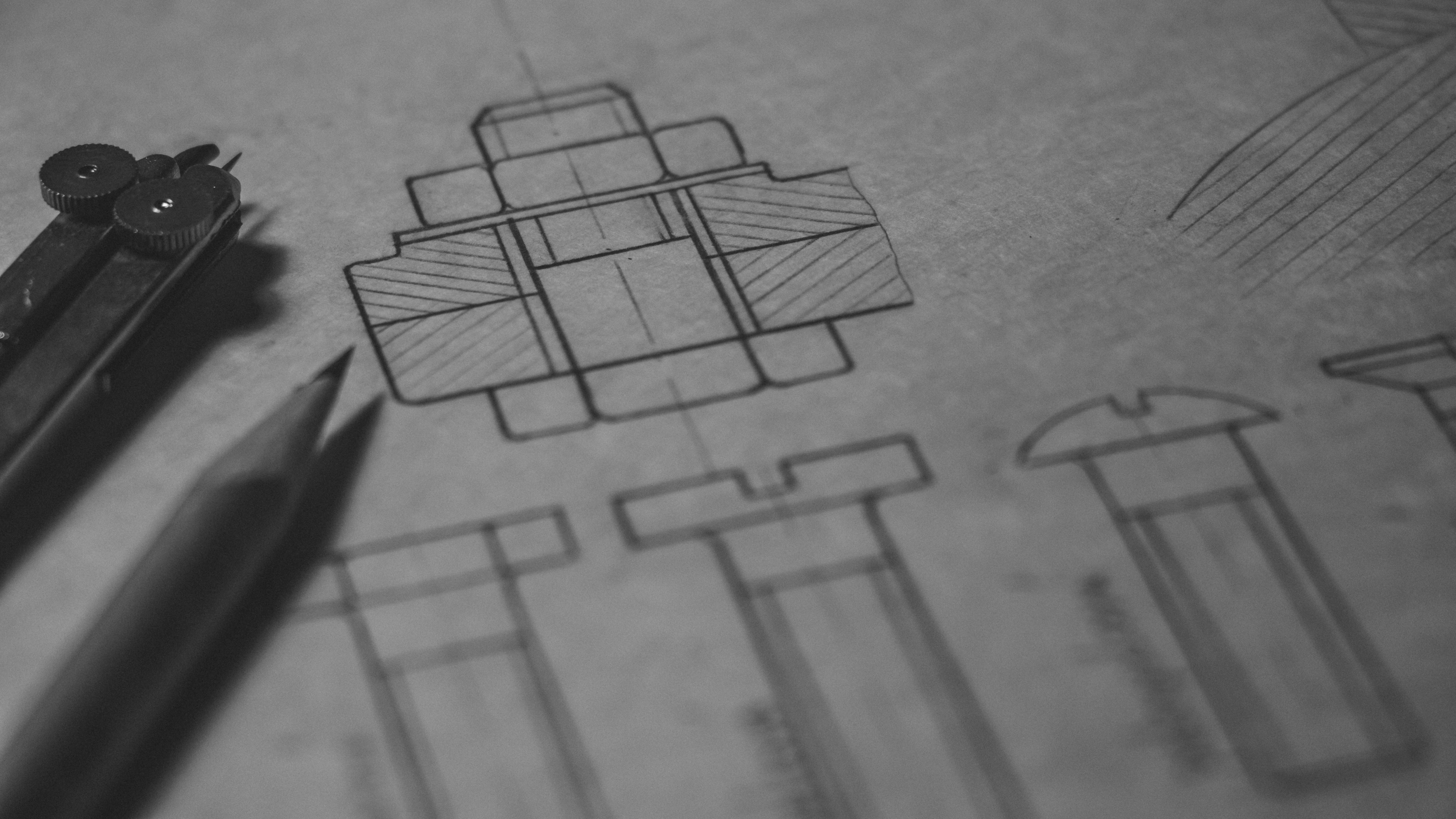