Mastering Mold Design for Precision and Efficiency
Aug 3, 2023
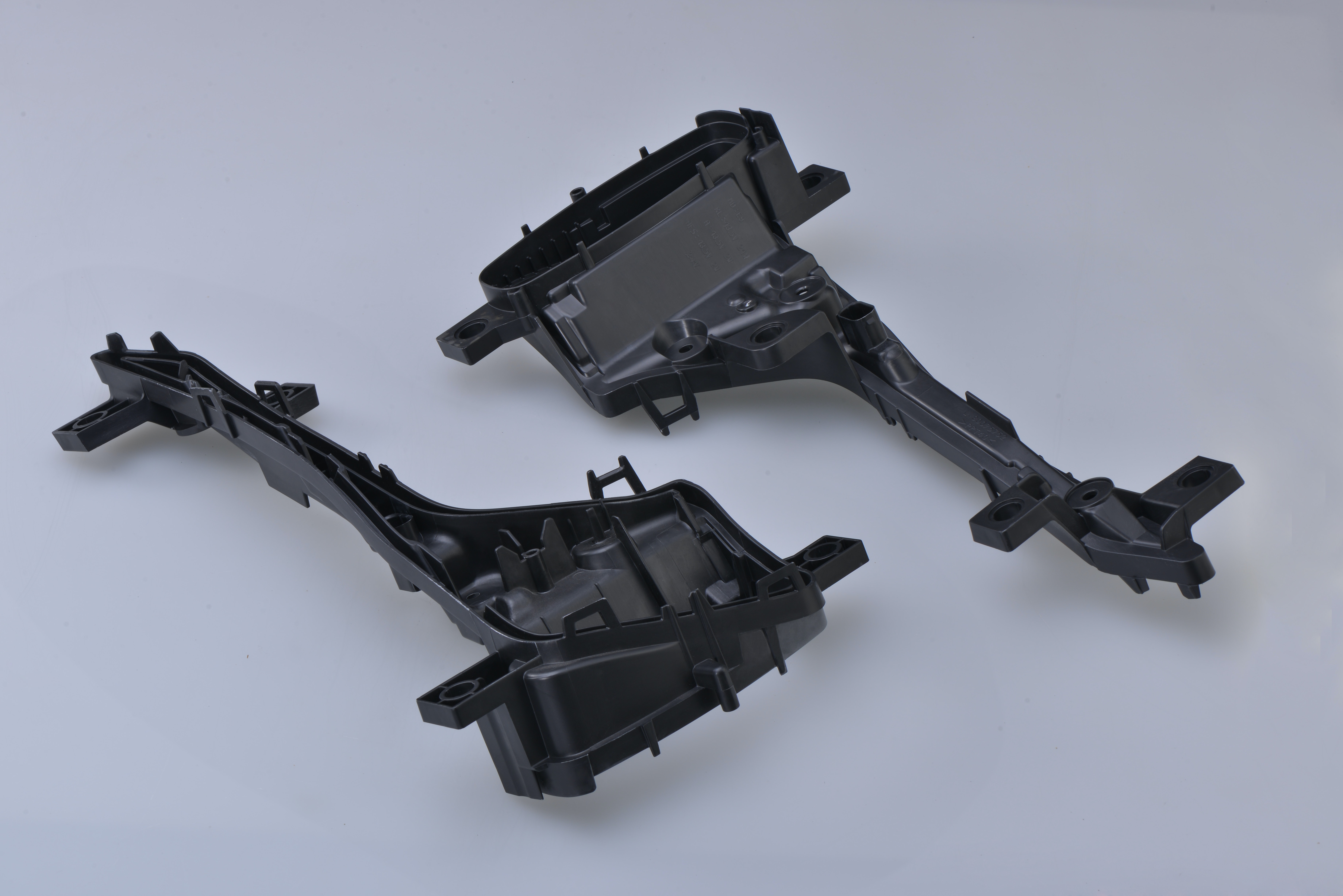
Injection molding is as much an art as it is a science. At the heart of this process lies the mold design – a critical element that directly influences both the efficiency of the molding process and the quality of the final product. In this article, we'll delve into the intricate aspects of mold design, highlighting the factors that drive precision and enhance production efficiency.
Gate Placement: The Gateway to Quality
The gate is the point where molten plastic enters the mold cavity. Its size, shape, and location can dramatically affect the final product's appearance, structural integrity, and even the molding cycle time.
Strategically Positioned Gates: Proper gate placement ensures even flow of plastic, reducing the chances of air traps, weld lines, and other defects.
Optimal Gate Size: An appropriately sized gate ensures swift and efficient filling of the mold cavity while minimizing stress and potential warping of the part.
Venting: Breathing Life into Precision
Without proper venting, trapped air can create burn marks or incomplete fills. Venting plays a pivotal role in ensuring a flawless finish.
Strategic Vent Placement: Vents are usually positioned at the mold's parting line or the last place to fill in the cavity. They allow trapped gases a safe exit, preventing defects.
Vent Depth Considerations: Too deep and you risk flash defects; too shallow and you risk inadequate venting. It's a delicate balance to strike.
Wall Thickness: The Backbone of Structural Integrity
Mold wall thickness impacts the cooling time, shrinkage rate, and the structural strength of the final product.
Uniform Thickness: Keeping wall thickness uniform helps in even cooling, thus reducing warping and internal stresses.
Thick vs. Thin: While thicker walls provide strength, they increase cycle times and can lead to sink marks. On the other hand, overly thin walls might compromise the part's strength and can pose challenges in mold filling.
Cooling System Design: The Unsung Hero of Efficiency
A well-designed cooling system drastically reduces cycle times and ensures the production of consistently high-quality parts.
Efficient Cooling Channels: Properly spaced and adequately sized cooling channels ensure rapid and even cooling, a critical factor in maximizing productivity.
Temperature Control: An effective cooling system design, combined with optimal temperature control, can reduce shrinkage, warping, and other defects.
In conclusion, mold design is a meticulous process that demands a deep understanding of the intricacies of injection molding. At WSCC, our expertise in mold design ensures that every component we produce not only meets but often exceeds our clients' expectations. By focusing on the nuances of mold design, we guarantee both precision and efficiency in every project.
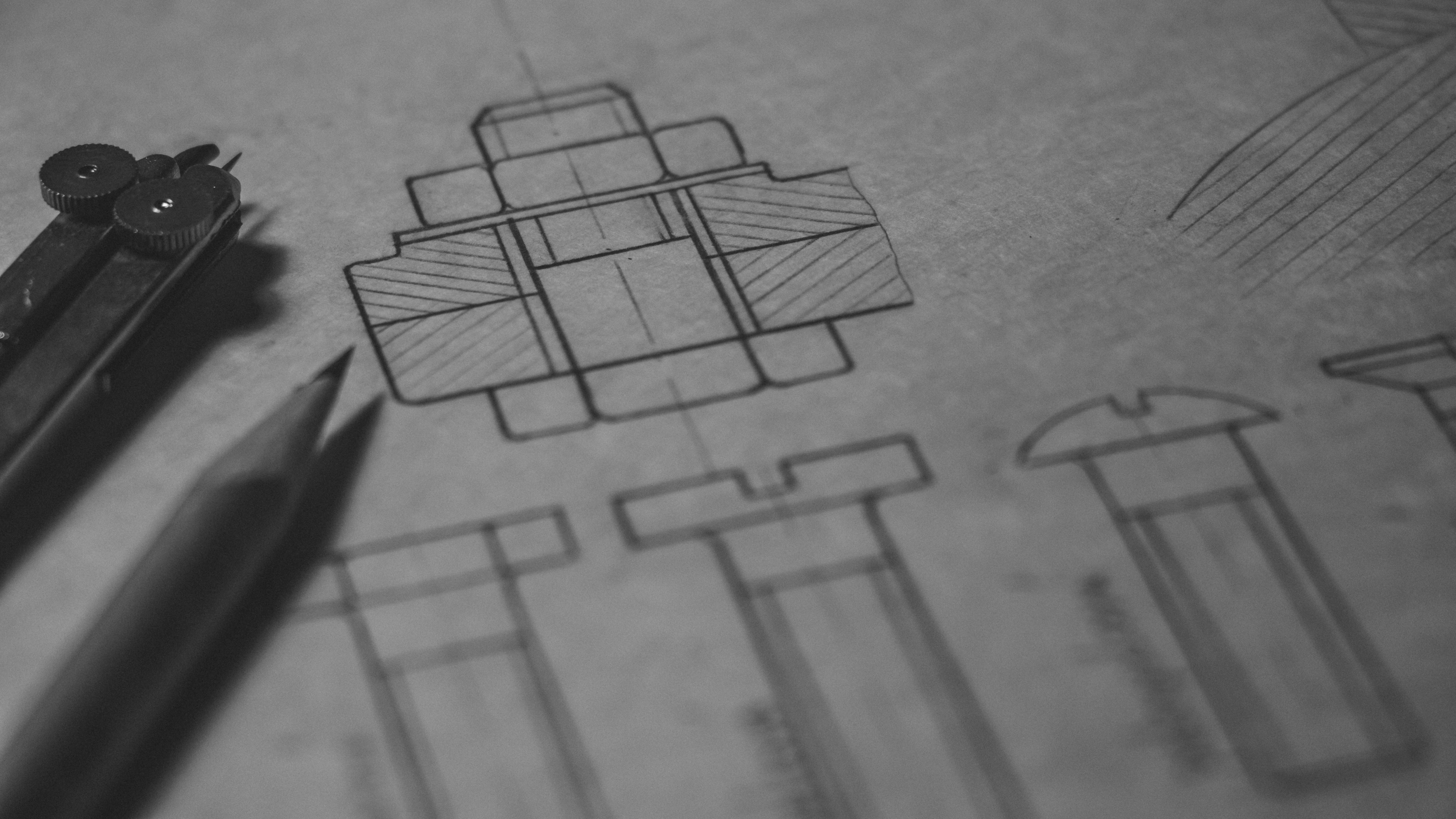