The Evolution of CNC Machining
Sep 28, 2023
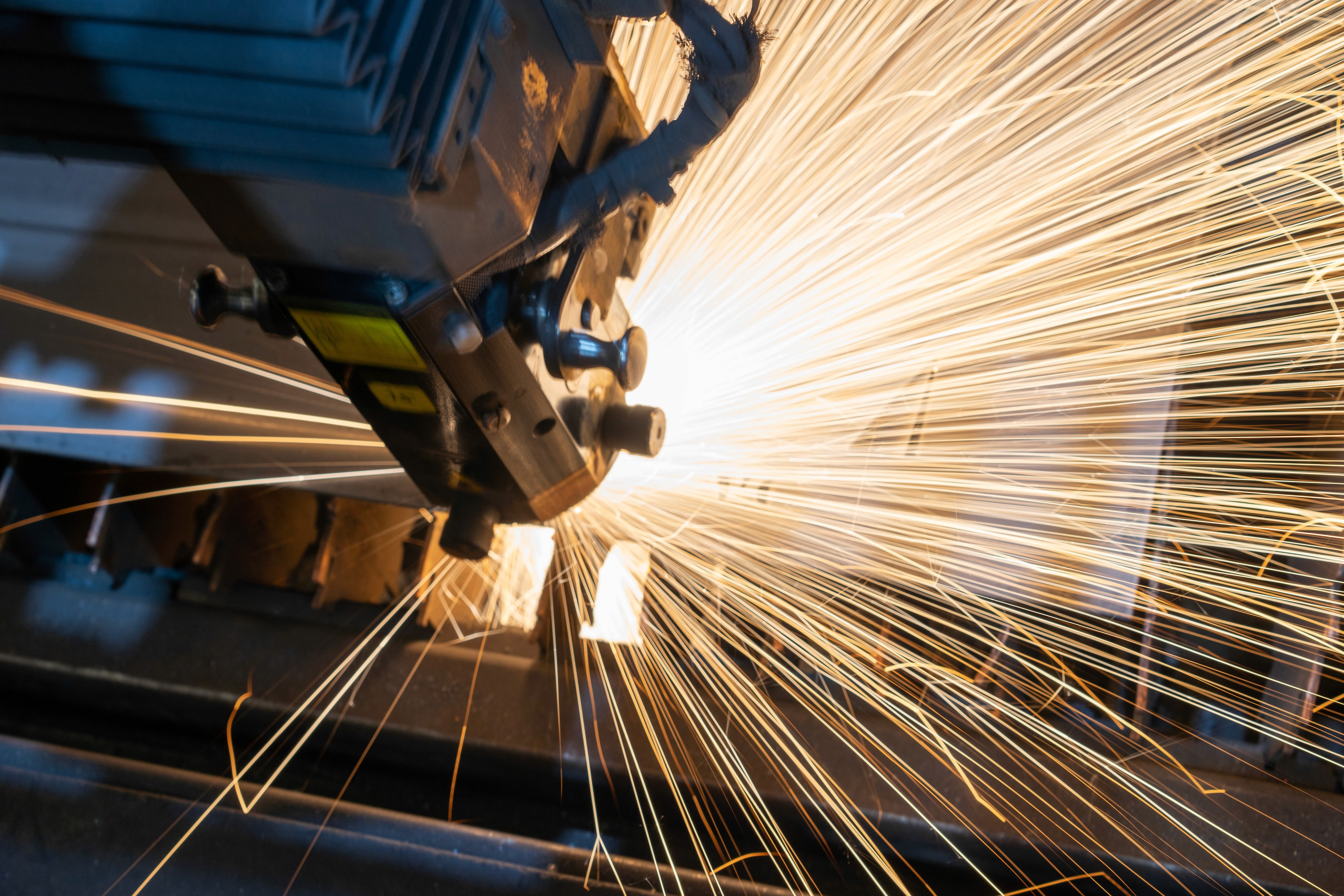
CNC (Computer Numerical Control) machining has fundamentally transformed the landscape of manufacturing over the past few decades. With roots in the early numeric control systems of the 1940s, CNC has grown into an indispensable tool for modern production environments. Let's take a journey through the evolution of CNC machining, tracing its development from rudimentary beginnings to today's advanced capabilities.
1. The Humble Beginnings: Punched Tapes and Early Numeric Control (NC)
In the 1940s and 1950s, early NC machines operated using punched tape to guide their movements. These precursors to modern CNC systems, while primitive by today's standards, marked the first steps in automating machine tools, freeing them from the limitations of manual control.
2. Birth of True CNC: Integrating Computers
The 1960s and 1970s saw the integration of computers into the mix, giving rise to the term "CNC." These systems offered more flexibility than their predecessors. With storage capabilities and programming potential, they revolutionized manufacturing processes, paving the way for intricate designs that were previously deemed unachievable.
3. The Software Surge: CAD/CAM Integration
The 1980s and 1990s witnessed the fusion of CNC machinery with CAD (Computer-Aided Design) and CAM (Computer-Aided Manufacturing) systems. This integration allowed for smoother transitions from design to production, reducing lead times and enhancing precision.
4. Multi-Axis Magic: Beyond 3D Manufacturing
As the 21st century dawned, CNC machines evolved from three-axis (X, Y, Z) to multi-axis capabilities, including 4-axis, 5-axis, and even 6-axis machines. This advancement expanded the possibilities of what could be created, allowing for complex geometries and reducing the need for tool changes and setups.
5. Connectivity and the Cloud: CNC in the Era of IoT
Today, CNC machines can connect to the Internet of Things (IoT), streamlining maintenance, monitoring, and even remote operation. Cloud-connected CNCs can share data, optimize operations based on real-time insights, and facilitate collaborative manufacturing across various locations.
6. Looking Ahead: AI, Automation, and Adaptive Machining
The future of CNC promises even more innovation. With the integration of artificial intelligence (AI) and machine learning, CNC systems can adapt in real-time, optimizing for tool wear and unforeseen variables. Moreover, as automation becomes more prevalent, CNC machines will likely play central roles in fully automated production lines, pushing the boundaries of efficiency and precision.
The journey of CNC machining from its inception to its current state is a testament to human ingenuity and the relentless drive for progress. At WSCC, we embrace the rich history of CNC while eagerly anticipating its future, ensuring we remain at the cutting edge of manufacturing excellence.
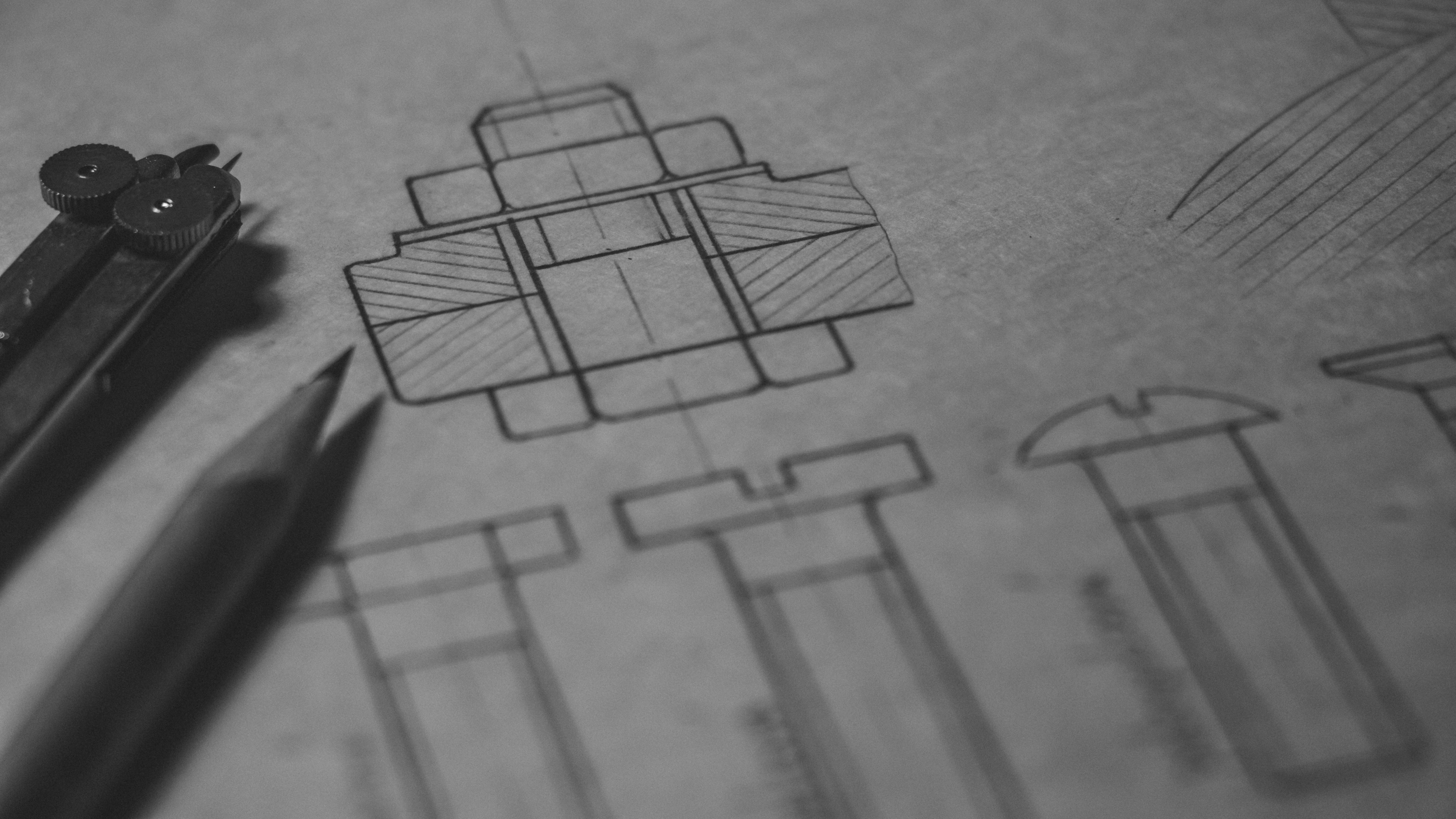